CAO
Why is flying so safe? Control engineering in action.
CAO
Why is flying so safe? Control engineering in action.
Flying a modern passenger jet is a ‘collaborative’ task between the human pilot and the computer.
It’s what makes flying so safe, and for an industry that successfully serves over 1 billion people a year, it needs to be so. But how exactly do we manage to make it so safe?
Control engineering is the answer.
It’s all down to the so-called ‘fly-by-wire’ technology, grounded in control theory. But to understand what fly-by-wire actually means, we’ll first need to look at the basics. That is, how a plane works and the devices that control engineering can regulate.
The basics
To control an aircraft, pilots move the flight stick and the rudder pedals.
The flight stick is similar to the steering wheel of a car as it can be moved in any direction the pilot wishes to take.
The rudder pedals are used to keep the aircraft nose aligned with the direction it is heading toward. The rudder pedals are positioned similar to that of the gas and brake pedals on a car.
Originally, aircraft used manually operated mechanisms to fly the plane (some still do).
The flight stick and pedals would be mechanically linked to the flight control surfaces. These surfaces allow the plane to move in the appropriate way via cables and pulleys. They include the elevators which make the plane ascend and descend, and the ailerons and rudder which make the plane turn.
Any movement exerted by the pilot would be instantly transferred to these control devices, causing a manual change in the aircraft’s trajectory.
But in a modern fly-by-wire aircraft, it’s a little different.
In this case, the pilot’s inputs are not mechanically linked to these control surfaces. Instead, a flight control computer stands between them.
Movements in the flight stick and pedals are converted into electrical signals, which are sent to the on-board computer. The computer does thousands of calculations every second. It determines the best way to move the control surfaces according to what the pilot has inputted.
The message is then sent via electrical wiring to the control devices to enable the plane to move, giving us the term ‘fly-by-wire’ technology.
Manual vs. fly-by-wire?
It is no surprise that aircraft technology has become more computer-based. For aviation, the reason behind this is simple: it makes flying safer. Not only just safer, but with increased comfort during a flight in both passenger aircraft and military air travel.
Avoid dangerous attitudes
Aircraft attitude refers to the orientation of the aircraft with regard to the horizon. In a passenger aircraft, the flight control computer is programmed to prevent the pilot from inadvertently putting the aircraft at a dangerous attitude. If the pilot attempts to raise the aircraft’s nose up beyond 30 degrees, for instance, the computer will ignore the command and keep the nose below.
Fighter jets rely on the same technology to achieve high manoeuvrability.
This is because the control surfaces (elevators, ailerons, rudders) on these jets are extremely sensitive. An incorrect movement by a couple of degrees can lead to a total loss of control in less than a second. Flying these fast jets requires as many as 40 small adjustments every second – something that only a computer could do so quickly.
Increased comfort
Modern large passenger jets tend to have more control surfaces beyond the traditional elevator-aileron-rudder combination. They perform many functions, two of which are ‘gust alleviation’ and ‘gust load alleviation’. These control surfaces, referred to as spoilers, are automatically raised/lowered by a small amount to alter the aerodynamic load across different sections of the wing. By counteracting the momentum generated by a gust of wind or turbulence for example, these systems can improve passenger ride comfort (gust alleviation). They also reduce the structural load on the aircraft structures (gust load alleviation).
Both systems are operated at all times during a flight. The flight control computer manages the required control surfaces without pilot intervention. When the wheels touch the ground, the spoilers are fully raised to generate as much drag as possible, which helps slow the aircraft down. The clip below demonstrates gust and gust load alleviation on a large passenger jet.
Challenges
As with any technological breakthrough there are challenges with these sorts of control systems. Any new developments and algorithms as well as their associated hardware and sensors must be designed and tested by large and multidisciplinary teams of engineers. Only then can they be put into use by the aviation industry.
See below a clip of a 1989 crash – a pilot-induced oscillation caused by excessive lag in the fly-by-wire system and actuator rate limiting. The pilot, Lars Rådeström escaped with a fractured elbow and some minor injuries.
With self-flying air taxis and drones on the horizon, the emphasis on safe and efficient flying is more important than ever. Control engineers play an important role in bringing these projects closer to reality using fly-by-wire.
Duc Nguyen(Opens in a new window) is a tutor for the University of Cambridge Online(Opens in a new window) course ‘Control Engineering.’ He is also a current Research Associate at the University of Bristol.
Ready to start your control engineering journey? Find out more about the course and how it might be useful in your professional context here: https://bit.ly/3XcEqdt(Opens in a new window)
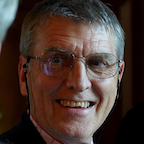